Chromatic aberration is a term used to describe the difference in color observed in products, such as in the printing industry, where printed products may differ in color from a standard sample provided by a customer. Accurate evaluation of chromatic aberration is crucial in the field of industry and commerce. However, various factors such as light source, viewing angle, and observer's condition can impact color evaluation, resulting in color differences.
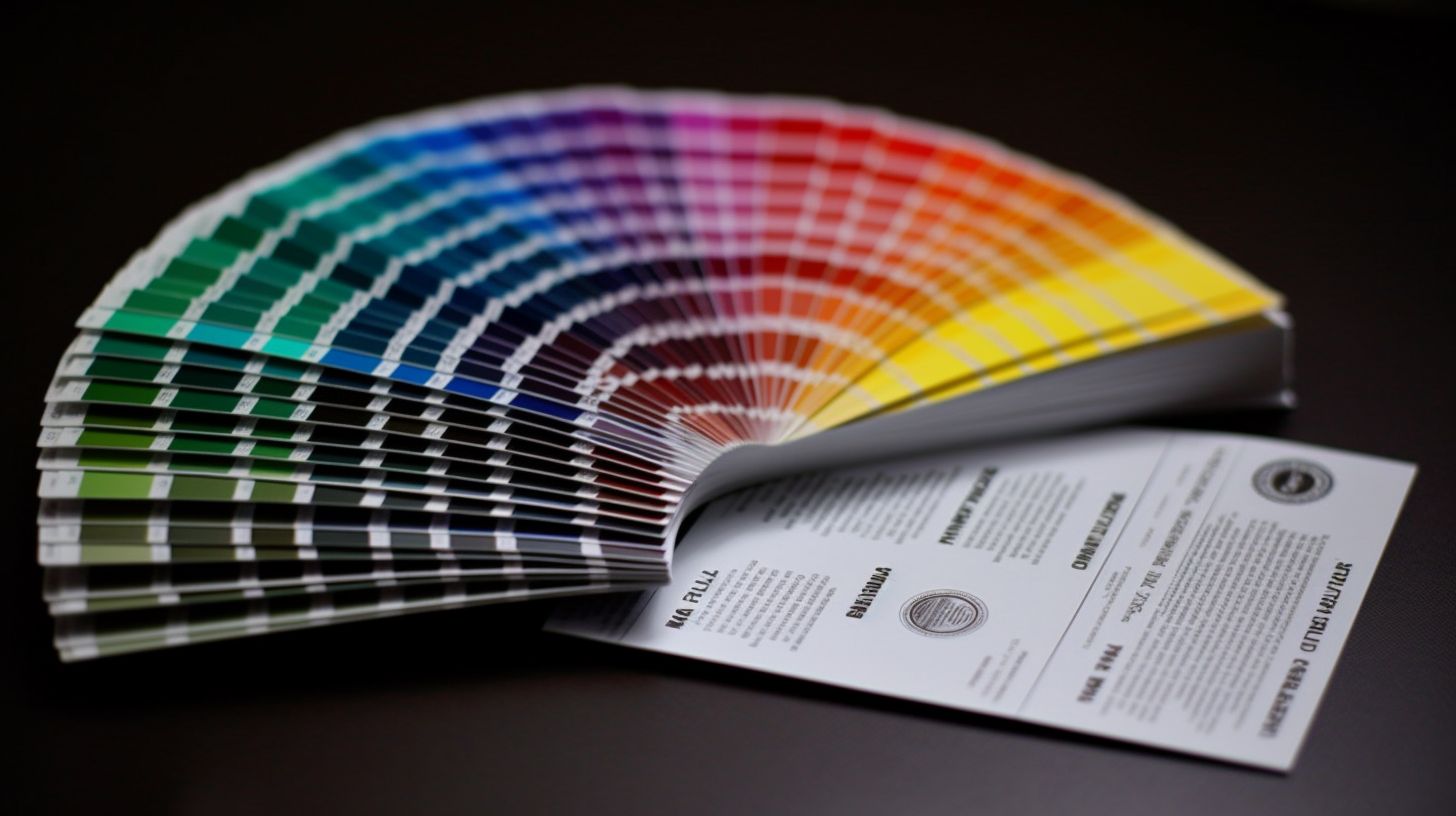
To control color differences and achieve color accuracy in printing, it is important to consider six key elements in the printing process.
Color Mixing: Many printing technicians rely on experience or personal judgment to adjust colors, which can be subjective and inconsistent. It is important to establish a standard and unified approach to color mixing. The use of printing inks from the same manufacturer is recommended to prevent color deviations. Before color mixing, the color of the printing ink should be checked against the identification card and accurately measured using proper weighing and metering methods. The accuracy of data in the color mixing process is critical for achieving consistent color reproduction.
Printing Scraper: Proper adjustment of the angle and position of the printing scraper is important for the normal transfer of printing ink and color reproduction. The angle of the ink scraper should typically be between 50 and 60 degrees, and the left, middle, and right ink layers should be scraped symmetrically. It is also important to ensure that the scraping knife is clean and balanced to maintain color stability during printing.
Viscosity Adjustment: The viscosity of the printing ink should be carefully regulated before the production process. It is recommended to adjust viscosity based on the expected production speed and thoroughly mix the ink with solvents before starting the production process. Regular viscosity testing during production and accurate recording of viscosity values can help in adjusting the entire production process and minimize color deviations caused by changes in viscosity. It is important to use proper viscosity testing techniques, such as using clean viscosity cups and conducting regular sample inspections to ensure quality.
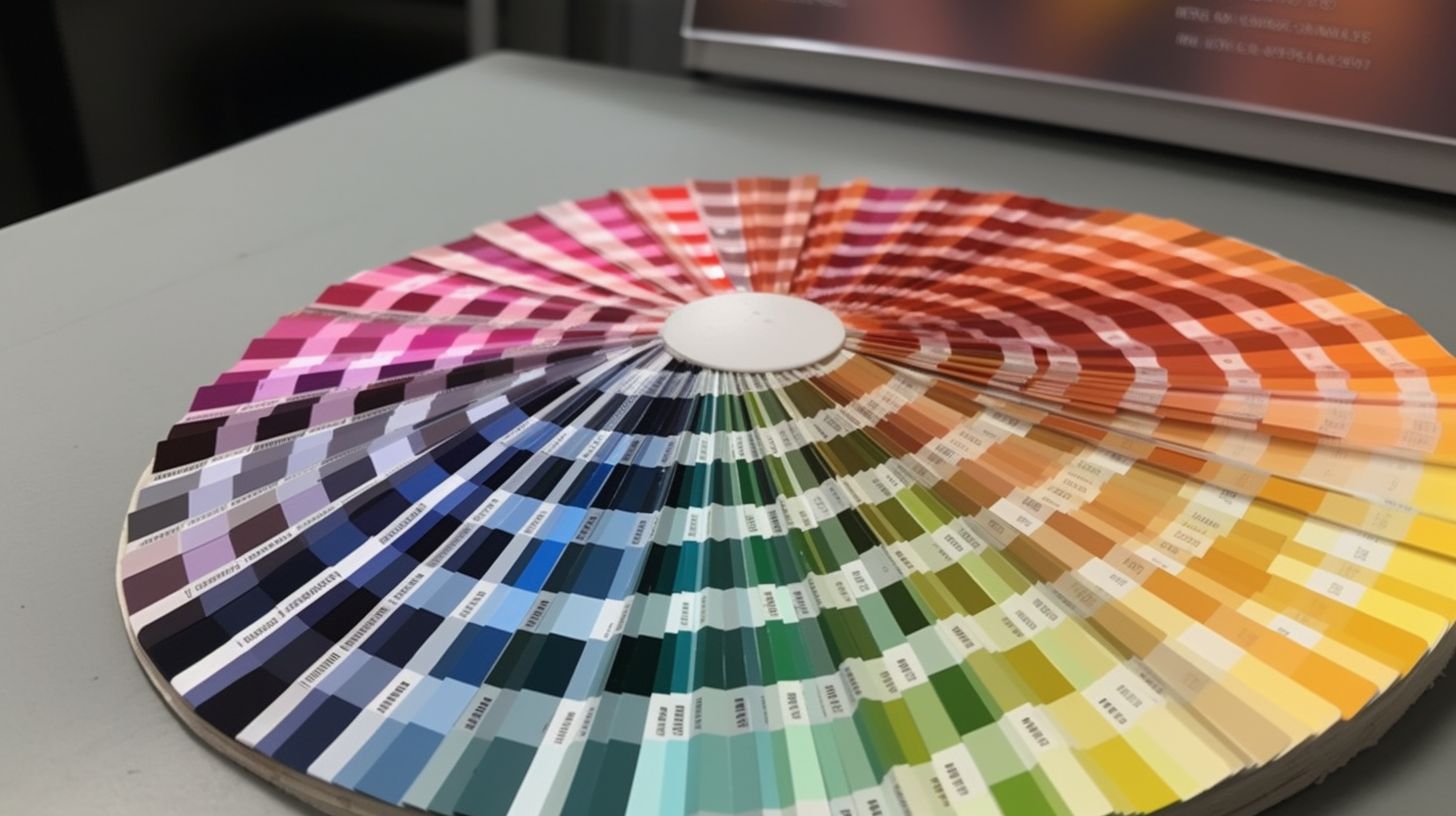
Production Environment: The air humidity in the workshop should be regulated to an appropriate level, typically between 55% to 65%. High humidity can affect the solubility of printing ink, especially in shallow screen areas, leading to poor ink transfer and color reproduction. Maintaining the proper humidity level in the production environment can improve ink printing effects and minimize color differences.
Raw Materials: The surface tension of raw materials used in the printing process can also impact color accuracy. It is important to use raw materials with qualified surface tension to ensure proper ink adhesion and color reproduction. Regular testing and inspection of raw materials for surface tension should be conducted to maintain quality standards.
Standard Light Source: When checking colors, it is important to use the same standard light source for color viewing or comparison. Colors may appear differently under different light sources, and using a standard light source can help ensure consistent color evaluation and minimize color discrepancies.
In conclusion, achieving accurate color reproduction in printing requires attention to various elements, including proper color mixing techniques, careful adjustment of printing scraper, viscosity regulation, maintaining the appropriate production environment, using qualified raw materials, and using standard light sources for color evaluation. By implementing these best practices, printing companies can optimize their printing processes and minimize chromatic aberration, resulting in high-quality printed products that closely match the design drafts.
Post time: May-05-2023